Reflections on the Immerse Technology Conference
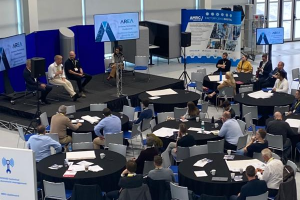
As the dust settles on the latest conference season, I wanted to share my reflections and excitement as we resume conducting face-to-face AR events across the world.
As an evangelist for enterprise Augmented Reality, I know that one of the best ways for people to understand what AR is, what business problems it solves, and how will it benefit their work is to experience the solution in person. That’s what made the recent Immerse Technology Conference on September 28 and 29 such a successful event.
The AREA hosted the conference with partners Innovate UK KTN, Made Smarter Innovation Network, Immerse UK and the High-Value Manufacturing Catapult (HVMC). It was held in Factory 2050, located in the Advanced Manufacturing Resource Centre (AMRC), University of Sheffield, Sheffield, UK, a longstanding AREA member.
Many thanks to Gold sponsors Magic Leap, Rockwell Automation, Augmental, and Team Viewer, as well as our Bronze sponsors Assured Cyber Protection, Realwear, ESI Group, and support from Microsoft.
More than 100 attendees were on hand, providing many opportunities for demonstrations and hands-on workshops defining the benefits and challenges of deploying AR technology.
Day 1 started with an introduction from the host companies followed by excellent thought leadership presentations from companies who have successfully deployed AR. Boeing, Siemens, and Rolls Royce highlighted the work and benefits they have gained from the successful and wide deployment of AR.
Magic Leap then presented and launched the Magic Leap 2 in the UK with a presentation on its new features and go-to-market strategy. Rockwell Automation also provided an insightful presentation titled “Extended Reality and its Role in Digital Manufacturing”.
The rest of Day 1 focused on workshops, led by Augmental and Magic Leap, in which attendees learned about the AREA tool “Enterprise AR Use Case Development Framework” to help understand AR/VR Uses Cases and Requirements. This interactive session was enjoyed by all the participants and offered a great opportunity to learn from experts and discuss key use cases.
Finally, there was more time to experience the excellent demos from the sponsors and engage in some informal networking. We’d packed a great deal of content into Day 1 – but there was much more to come.
We began Day 2 with a thought leadership presentation from ESI Group, “Industry 4.0 Drivers for VR Democratization,” followed by one on the key challenges for implementation, building an AR workforce. A panel of experts from Realwear, Boeing, and Rockwell Automation discussed tactics and tools to convince stakeholders in a company to invest in AR solutions and how to overcome end user concerns.
Augmental followed with an excellent presentation on a process to help companies deploy AR and a case study from technology partner holo|one.
Creating a Return on Investment (RoI) model is often a challenge, but in the next session, the AREA showed how to overcome it using the free AREA RoI Calculator. The session covered the background of the calculator, how to use it, and an introduction of AR cases studies that demonstrated a clear RoI. The presentation from Strategy Analytics helped the attendees understand and plan future RoI analysis.
Two more thought leadership presentations from Team Viewer and Realwear led the way before interactive sessions on Human Factors and Related Safety Challenges, and “Security is Key: Overcoming the Challenges of AR Security”. The event concluded with a set of three-minute pitches from immersive tech providers on their solutions and “Understanding Virtual Reality Use Cases, Requirements & Research”.
Feedback from attendees was excellent, with many of them appreciating having the ability to experience, interact with, and learn from the AREA members, giving them a clearer understanding of how to deploy AR.
When it was all over, participants had learned:
- How to overcome barriers to the adoption of AR within an organization
- Use cases and requirements for enterprise AR
- Commonly encountered safety risks and how to manage them
- Security risks associated with AR-enabling technologies
- Techniques for managing change, stakeholders, and staff challenges when introducing AR
- UX design and development for VR and AR apps
Based on that success, we are now in the midst of planning future similar events in Europe (Q1 ’23), the US (Q2), and the UK (Q3). If you have any questions regarding the event – or would like to participate in our future conferences – please contact me (mark@thearea.org).