Magic Leap’s Augmented Reality 101 What It is and How It Works
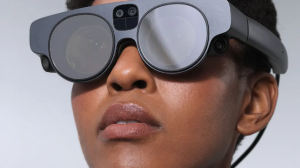
What augmented reality means
“Augmented” reality is an everyday reality that has been augmented or enhanced by the addition of digital visual information. The image you see in AR is exactly what you see in the real world using your eyes, but with images and text overlaid within your field of view via a wearable device. AR is different from “virtual” reality (VR), in which the user is fully immersed in a digital experience with the headset blocking out the external world completely.
The concept is so widespread that chances are you’ve seen or experienced AR in a basic form. When Iron Man looks through his visor and sees computer readouts alerting him to danger, that’s a form of AR, albeit one filtered through a fictional comic book or movie framework.
In the real world, the mobile game Pokemon Go incorporates augmented reality elements by using your phone’s camera to superimpose cute critters into the real world around you. Snapchat filters are another well known example that you may not think of as augmented reality.
While virtual reality shuts you off from the outside world, requiring new environments to be built, augmented reality integrates digital content into your physical environment.
These examples deliver an impressive, entry-level AR experience using the basic technology available in smartphones. Now imagine what’s possible with a lightweight, wearable computer created specifically with augmented reality in mind– one that can integrate digital content that is contextually aware of the physical environment it’s in.
How augmented reality works
Augmented reality works by analyzing the environment and using triggers around you to display relevant information in the applicable place in your field of view. So, for example, an AR function for a map application might be programmed to detect the logos of specific stores and display details such as store hours when you look at them.
On a smartphone, that’s simply a case of putting the information on the screen. But for a wearable AR headset like Magic Leap, the process is even more immersive. By using information from the built-in eye tracker, virtual content is rendered correctly and slightly differently for each eye, which enables virtual objects to appear at any depth.
Designed for comfort and long-term use
Enterprise-class, head-mounted displays must be designed in a way that lets the user wear them for longer periods of time without causing fatigue or strain. Because the device must fit securely and perform well, Magic Leap did the work to measure performance and comfort on a diverse range of users.
Researchers at Magic Leap spent years capturing 3D scans of hundreds of heads and have seen a wide range of head shapes, sizes, distances between nose bridges and eyes, all to inform the industrial design of the platform. Numerous pad configurations for forehead and nose make Magic Leap comfortable for all head shapes and sizes.
Magic Leap devices are fully customizable, distribute weight evenly around the head, and are designed for thermal comfort. You can even insert prescription lenses into your device to make it even more customized.
Designed for human physiology
Magic Leap has a unique heritage of designing for the human body thanks to the founding team’s groundbreaking work in the biomedical industry. This experience has uniquely inspired Magic Leap to create a device that operates harmoniously with human physiology.
Magic Leap works in tandem with our natural visual system in a safe and effective way to create incredibly real experiences. Magic Leap’s operating range begins at 37 centimeters, well within an arm’s length, and is among the largest operating ranges in the industry. Accordingly, Magic Leap has designed its AR wearable devices to deliver experiences that are low friction and do not typically induce nausea.
How augmented reality can be used
By bridging the divide between the digital and physical worlds, and combining them in a unique first-person point of view, AR has the potential to revolutionize many different professional fields, not just personal entertainment.
AR allows doctors to plan for complex surgical cases
Augmented reality is already being used in cutting-edge medical scenarios. In October 2020, surgeons at UC Davis Children’s Hospital in Sacramento, CA, used Magic Leap technology to prepare for the separation of twin babies who were joined at the head. This rare and intricate surgery was planned by building a 3D reconstruction of the conjoined twins from MRI and CT scans, which were then viewed on the Magic Leap platform using Brainlab’s Mixed Reality Viewer software. The surgical team was then able to walk around the models to view all possible angles before a single incision was made.
SentiAR’s software, for example, connects operating physicians to 3D patient cardiac data in real time helping guide them during the procedure. It also helps patients visualize and understand the procedures they are about to undergo. SyncThink, Inc. is another company working with Magic Leap on clinical trials to explore AR for vestibular disorders like concussions. Heru, Inc., on the other hand, is using AR to innovate diagnostic solutions in optometry. The company’s platform on the Magic Leap 2 headset is designed to replace several legacy diagnostic devices and includes planned applications related to personalized vision correction that would allow clinicians to diagnose and manage patients with increased efficiency.
There are everyday practical applications as well, allowing doctors to view patient notes remotely, or collaborate with colleagues on patient cases in different cities or even countries.
Manufacturing problems can be tackled remotely
Linear motion company PBC Linear is one of the many organizations using AR to capture and leverage machine instructions from seasoned employees and train new machine operators, resulting in an 80% reduction in training time and 20% in annual savings due to less scrap and fewer mistakes — ensuring quality parts get to customers on time. Thanks to an AR package called Manifest, created by Taqtile and running on the Magic Leap platform, PBC Linear frontline workers have instant access to step-by-step guidance from their most experienced technicians and trainers, anytime and anywhere. AR is helping train and upskill the PBC Linear workforce, regardless of geographic location.
Shared digital spaces can shake up enterprise and marketing
Created to work in both physical and virtual shared spaces, the potential uses for augmented reality are limited only by ambition and imagination. Magic Leap is used by enterprise platforms such as Cavrnus, which collaborated with events agency Fix8Group to produce a hybrid model for experiential brand marketing in which in-person attendees, and those joining via AR, were able to communicate, collaborate, and even influence the lighting and music.
Magic Leap is also used by Talespin, an immersive learning platform that uses AR to deliver corporate skills training, and by “data storytelling” company Flow Immersive, which transforms complex information into easily understood AR visualizations that are shareable on social media.
The future of augmented reality?
A March 2021 study by Statista estimated there will be 2.4 billion mobile AR users worldwide by 2023. Ownership of dedicated AR devices such as Magic Leap is expected to reach 30 million units by 2023, an increase of over 380% from 2020. Increased use of AR platforms is one thing, but as the saying goes, you should follow the money for the full story. Spending on “extended reality” technology for just the U.S. construction and manufacturing sectors is projected to hit $35 billion in the next two years.
Unlike virtual reality, AR’s hybrid nature means that it is far more adaptable to real-world applications and that is only going to become more apparent as platforms evolve and developers discover new ways to overlap the virtual and real worlds.