Norwegian Agricultural Heavy Machinery Manufacturer Orkel Grows with RealWear Assisted Reality Devices
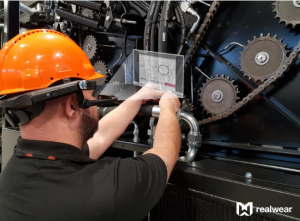
The company’s initial purchase of 40 units through RealWear’s Gold partner Allegra AS, will be used for remote after-sales maintenance, remote servicing and remote commissioning of all its heavy agricultural machinery products. Orkel’s research and development team tested a variety of smart glasses before standardising on RealWear’s HMT-1® head-mounted displays. According to Orkel, RealWear’s rugged form factor, safety features, noise cancellation and long battery life were deciding factors.
How the Solution Works
The innovative solution allows Orkel to connect its customers to its service technicians without the need for unnecessary travel. As part of Orkel’s after-sales support offering, each customer in need of commissioning or a technical service receives a kit consisting of the HMT-1, a branded Orkel hardhat, and mounting clips. The customer simply puts on the device, contacts the Orkel technician using voice commands and, after connecting, the technician can immediately see exactly what the customer sees through the head-mounted camera and easy to use software – VSight. The technician then solves the issue. Once resolved, the customer may then choose to purchase the RealWear device for their own use or return it to Orkel.
The solution solved a number of pain points for Orkel. For instance, typically its service technicians were required to make an in-person customer trip, which involves travel time and environmental costs. A delay in fixing the equipment also has the potential to impact the customers’ businesses.
“Our customers really appreciate the value of the system because we are able to provide a much faster level of support when an issue arises. All too often, our service technicians would travel for what turned out to be a quick fix. Now, with RealWear, many hours of time and CO2 emissions are saved, and most importantly customers’ machines are operational again quickly, which is imperative during the harvest season,” commented Svein Erik Syrstad, Technician, Orkel.
Headquartered in Fannrem, Norway, Orkel Group is an established supplier of compactors, round balers and transport equipment. With a presence in more than 50 countries across the globe, its biggest market currently is mainland China. As the farming and agriculture sectors are heavily dependent on the harvest season, Orkel’s customer base requires maximum uptime from their Orkel machinery, especially during the busy season.
On the device, Orkel is using RealWear partner VSight Remote, a remote service and collaboration platform powered by AR that helps manufacturing companies conduct maintenance operations remotely with Augmented Reality. The Orkel machine’s telemetry system ensures that details about every aspect of the machine’s operation is sent securely to the cloud, enabling Orkel’s service technicians to read the data and guide their customers to the next step in the procedure. This information enables Orkel to target the specific error more efficiently, and then guide the operator remotely to resolution.
“We really adore this technology because as a research & development engineer, I can watch the work being done,” said Magnus Nordås Lervik, Project Engineer, Orkel. “I’m quickly learning better ways to design future machinery as I’ve seen first-hand the common issues that arise, and how they are fixed.” Lervik continued, “Using this technology enables our research and development team to look ahead to how we might design products in the future from an operator’s perspective.”
“Orkel and its customers are achieving a number of benefits since deploying RealWear’s technology with VSight and Microsoft Teams,” added Jon Arnold, Vice President of EMEA, RealWear Inc. “When looking at the agricultural industry as a whole, machine downtime impacts productivity and efficiency, especially in shorter and shorter harvest seasons. Remote assistance with RealWear is becoming a gamechanger for the farming and agriculture industry when every second matters.”