Mars Petcare reimagines manufacturing operations and coaching using RealWear hands-free headsets with Microsoft Teams
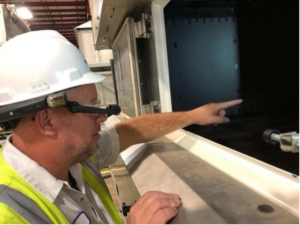
By investing in RealWear HMT-1 hands-free headsets equipped with Microsoft Teams, Mars Petcare found the perfect complement to its vision for more productive workplaces. Effortless, hands-free, and safer collaboration tools remain key to helping firstline associates at Mars Petcare become true equipment owners, making factories more productive and reducing travel and downtime due to maintenance.
Supporting autonomous maintenance with purpose-built technology
As Global Autonomous Maintenance Pillar Leader at Mars Petcare, one of David Oswald’s many responsibilities is autonomous maintenance. “As part of our Mars Supply Excellence program, we train and support our firstline teams to become true equipment owners responsible for the long-term reduction of losses. Our goal is to free up time on the shop floor to do the proactive work and make sure the equipment stays in a healthy condition.”
Through autonomous maintenance, Mars trains firstline associates to perform straightforward maintenance and preventative steps that keep equipment running like new—and keep factories at their most productive. The goal is for more streamlined factories and greater efficiency. “We say stop the stops,” says Oswald. “We target the short stops, such as resetting a machine or clearing a jam. We want an operator to run 240+ minutes without any intervention on their machine.”
Part of Oswald’s role requires finding the right technologies to support the Mars Supply Excellence program. To make collaboration effortless, he looks for highly mobile, hands-free devices designed specifically for the noisy, high-traffic reality of a manufacturing facility. That’s where RealWear hands-free headsets and Teams comes in, providing firstline associates on the factory floor tools that connect them to maintenance experts instantly for troubleshooting and training.
Teams on Realwear uses Teams meetings to power remote communication between HMT-1 users and their office-based colleagues. “The fact that the RealWear device works with Microsoft Teams was a big selling point for us,” says Oswald. “This allows us to connect associates on the shop floor with large numbers of people and collaborate in real time. Plus, the noise-canceling aspect of the ProBuds hearing-protection headphones and the hard-hat make it safe and ideal for the kinds of environments we work in.”
Other topics addressed in detail in the article include
- Keeping associates more safe and secure with the right tools
- Training and educating associates to drive efficiencies with new productivity tools
- Saving travel time and supporting sustainability
Read the whole article online at Microsoft