AR – Finding new ways to collaborate from a distance (Augumenta)
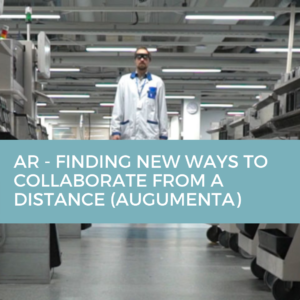
We are solving the problem
The Augumenta team develops wearables solutions that are used also for remote working and learning use cases. Our own working methods have enabled remote work since the very beginning of the company as the members are scattered around the globe in several locations and have always had the option of working from home. We have overcome challenges caused by different time zones and learned how to share and prioritize and support others in work tasks remotely.
And partly in the same boat
Having said that, we acknowledge that we face the same challenges as any other company during these times. We need to find new ways to collaborate with our customers on industrial augmented reality projects. Like most of you there, we cannot send our experts directly to customer locations to start projects and deliver solutions, and presenting your products entirely and only online is challenging. But we would like to encourage you, things can be done differently. There are ready-made solutions to support your experts in home offices and out there on the field.
How augmented reality and wearables can help?
In maintenance and repair, remote support with smartglasses and augmented reality have already a proven track record, and without a doubt helps save time and improve efficiency even during normal times. In manufacturing, the use cases expand into remote monitoring and machine control improving for example safety or uptime numbers. In training, smartglasses provide a tool for knowledge transfer and remote/independent learning. In fact, if there’s a need for any kind of support from an expert to another person working or learning in any field of industry, deploy smartglasses and AR apps.
Enhance the capabilities of local staff
With smartglasses and AR, you can improve the capabilities of workers to achieve things independently and even handle jobs that are not within their usual scope of tasks. This helps when there’s a shortage of skilled people available for certain tasks and experts can’t travel. Well-planned instructions and task lists with rich content that you can easily access while you work make practically any of us a semi-expert in many areas. If instructions don’t suffice a remote expert on the other side of a live video call that is sharing the same view gives you options to continue for example installation or repair projects that otherwise could significantly delay or not take place at all.
Learning-by-doing is the most efficient method of learning new tasks. Easy-to-use smartglasses apps and an experienced teacher giving remote advice is a highly efficient way of training new future experts, especially when you can’t be physically present in the same room. Smartglasses make a great tool for knowledge transfer. In simplest forms, they let an expert document the process of completing tasks correctly and share the result with less experienced colleagues.
With the right kind of devices and wearable apps accessing real-time IoT data, you can monitor and control processes and machines independent from your location. You don’t have to be in the control room or near a machine to get the alerts and notifications or the relevant values that you need to oversee a process. You can keep on working with other things/focus on fixing that one thing, and still rely on being notified of any upcoming issue requiring your attention. This makes a big difference if there’s a shortage of workforce and responsibilities need to be shared with utmost care so that those few capable can make sure all operations are running safely.
Today, the devices and applications can be controlled hands-free. This addresses also the problem of being able to work hygienically. You do not need to touch anything to get data in front of your eyes, control processes, or to document things. You can simply use gestures or voice to tell the device what to do. Tap air, not a keyboard.
In Augumenta, we’re used to dealing with industrial manufacturing, maintenance, and training people in those fields but the benefits of smartglasses and AR apply to any other industry area – including the medical field. Smartglasses can help medical staff, and not only now with their huge effort to take care of all the patients in the current situation, but also in the future by helping them to get the needed information in front of their eyes.
Changes in the way we work are here to stay
We cannot rely on going back to the old way of doing things once all of this is over, that’s for sure. There are lots of changes that stay and must stay permanent, how we work will affect the productivity and also sustainability of our operations. If you haven’t yet done it, now there’s no other option but to digitize operations.
We’d like to emphasize that there are tools and help available. We are most certainly having a bunch of applications that might help many of you and there’s quite a number of fellow AR companies with ready-made solutions available on the market. You can find a lot of information from the AREA organisation’s website.
Read Augumenta’s original article and their AREA member profile page.