Solving the Skills Crisis with Augmented Reality
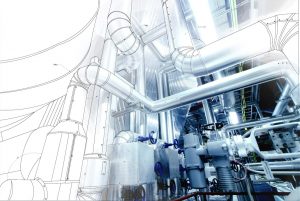
Where have all the workers gone?
The skills gap is the greatest threat to manufacturing today, second only to supply chain challenges: Nearly 45% of manufacturing leaders admit having turned down business due to lack of talent, while nearly half of frontline workers say the skills gap negatively impacts their productivity.
To understand why AR helps address the skills gap, it’s helpful to look at some of the factors that produced the gap in the first place:
Shrinking Workforce
Starting in the Eighties, a stigma around blue-collar work and the heightened importance of a college education led to fewer and fewer high school graduates joining the trades. Generational misconceptions about manufacturing work, automation and outsourcing, and the pandemic also contributed to the dwindling talent pool. Now, as Baby Boomers age out of the workforce, younger generations aren’t replacing them.
Pace of Innovation
Technology like automation, robotics, and 3D printing are slowly moving people off the factory floor into roles demanding more advanced (digital) skills. At the same time, increasingly complex products and processes are raising skill requirements in manufacturing and turning the skills gap into a moving target.
Outdated Tools
Despite talk of smart factories, old equipment and paper-based processes remain in manufacturing: 81% of frontline workers still use paper for day-to-day tasks, while 76% rely on in-person communication. In most factories, machinery older than some workers is a common sight alongside newer electronics. This complicates digitization and training and turns off younger workers.
Ineffective Training
Today’s manufacturing workers describe a technology gap and training gap. Conventional training methods like classroom courses, shadowing, hands-on training, and written manuals are costly, limited to instructors’ availability, and insufficient for keeping up with the industry’s rising learning curve. Moreover, they’re unsuitable for digital natives.
New Tools for the Frontline
77% of frontline workers say they don’t have the technology they need to be productive. Optimizing these workers’ productivity is the first step to blunting the impact of the skills gap. Second is to replenish the workforce with faster training and reskilling, and third is to improve the industry’s image. Augmented Reality (AR) can accomplish all three.
Fact: Augmented Reality is Narrowing the Skills Gap
Augmented Reality presents critical, contextual information, real-time insight, and remote expertise to frontline workers at the point of need, directly in the user’s line of sight on industry-leading mobile devices and hands-free headsets. Augmented work instructions, 3D products, video tutorials, schematics, IoT data, and other digital content appear on top of the work environment, directing frontline workers to do the job efficiently and accurately the first time.
Applications
Remote Assistance
What if your senior technicians were accessible to less experienced workers anytime, anywhere? Using an AR-supporting device, a junior technician can instantly share her view of a machine with a remotely located SME. The SME sees what the tech sees (live) and can guide her through the task remotely, even annotate her screen for precision. Later, a recording of the session can be repurposed as training material.
AR-powered remote support improves first-time fix rates, reduces the need for follow-up visits, and allows senior employees who might otherwise retire the opportunity to continue offering their skills. Experts can assist more workers in one day through AR than they could traveling to each worksite, effectively scaling expertise across the workforce.
Knowledge Transfer
Another way to pass on domain expertise is to have SMEs record their actions on the job, documenting specific procedures to turn into AR training material and work instructions. By having senior technicians wear smart glasses to capture tacit institutional knowledge, new employees gain a database of best practices and standardized instructions that can be superimposed in the context of the machine or task at hand for reference.
Augmented Work Instructions
Today’s manufacturing workers often work with ambiguous, outdated paper-based instructions that are difficult to follow. This wastes time and increases the likelihood of errors. AR provides on-demand access to information and turns complex processes into fool-proof visual workflows that reduce inefficiencies, increase productivity, and improve accuracy.
Humans process visual information like AR-guided work instructions better than any other type of data. Frontline workers using AR instructions don’t need to be familiar with a particular machine to service it, so manufacturers can confidently assign tasks to employees regardless of experience.
Training
When you follow AR instructions to do a new task, you’re learning that task at the same time. This is learning by doing and how younger generations learn best. AR makes it possible to safely and effectively learn on the job, in a live production environment, with significantly less supervision or downtime. Having AR as a digital mentor frees up training resources while improving time to proficiency. Off the job, AR makes training available on-demand, visually demonstrating complex processes in a way that’s easier to grasp and more engaging than e-learning and can be consumed from anywhere.
Reskilling & Recruitment
AR enhances learning for new and seasoned workers alike. More than 100 million workers will need to find different occupations by 2030, as manual and operator positions are replaced by higher-skilled, knowledge-based roles. AR-enabled upskilling programs ensure workers don’t get left behind, aid retention, make the workforce more agile, and help convince young people that manufacturing is actually a high-tech, future-looking career.
The Future of AR in Manufacturing
The benefits of augmented reality are not theoretical. Adopters are seeing greater year-over-year improvements in training time, retention of skilled workers, and hiring costs. PTC customers report significant impact like productivity, safety, and quality despite labor shortages. Frontline workers feel the value, too, in the form of increased safety and higher productivity. By driving digital transformation into the hands of workers today, AR is creating a more resilient workforce capable of closing the skills gap once and for all.