3 Steps to a Successful AR Business case
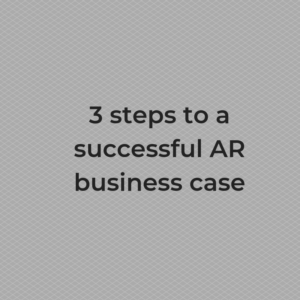
What do you want to achieve? And how does AR contribute to this? To get an overview of this, it helps to make a business case. It starts with discovering the value of AR. This blog helps you to get that clear.
The writer suggests starting at the value chain: a good start to discover your business case for AR is by first drawing up your own business processes and identifying where there is room for improvement. A good model for this is the Value Chain devised by Harvard professor Michael E. Porter. This model offers a schematic representation of the various departments. As the examples will show, augmented reality allows you to profit throughout the value chain of your company.
Questions to ask include what would you like the accomplish and does AR help with this?
The next section asks a series of questions to help you identify when AR can yield a profit.
- Do you want to convert poorly accessible teaching material into interactive 3D visuals?
- Do you have a shortage on technically qualified personnel and would you like experienced people to be in several places at once or watch juniors.
- Do you want to make it easier for R&D to bring prototypes to life and thus shorten the time-to-market of products?
- Are you looking for a tool that speeds up the sales process?
- Have you lost orders in the past because customers couldn’t clearly see if the product would fit before purchasing?
- Do you think storytelling is important? And do you want to take the user on a journey through unique features and show interesting details of your product that normally remain hidden to the naked eye?
- Do you want your measurement process to be easier and faster and have the measurement results immediately saved to a computer without noting down?
- Do you want to watch your customers remotely when your product has failed?
The author suggests that if the answer to any of the above questions is yes, then AR can help in your organization.